One of the things you see with a lot of high power projects are extensive use of fiberglass. A lot of scratch-built high power rockets use sono-tube as a basis, the fiberglass exterior gives it the strength to support the many Newton seconds of thrust required to make it fly.
Some even soak the cardboard out after they've laid up the fiberglass because it's relatively weak and relatively heavy.
So anyway, I bought some 3/4 oz fiberglass cloth and some 2 oz. And some fiberglass tape.
My first experiment was with the 3/4 oz stuff and it ended in frustration. I had read someplace that I should wet the surface with epoxy and then brush on the cloth with a brush impregnated with more epoxy, but this was not working. The brush wanted to take the cloth with it, my gloves got all tacky and it became impossible. I ended up stripping the cloth off and throwing it away.
My second try was with the fiberglass tape, small pieces of it at the fin joints of Kandy Kolored Tangerine Flake Streamline Baby's booster.
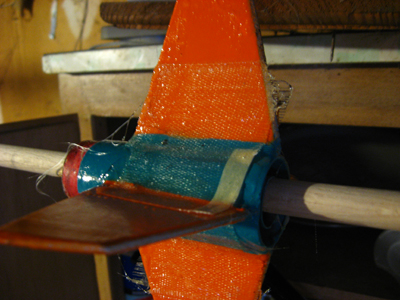
The booster tumbles away after it's spent, maybe 75 to 100 feet up in the air. And every flight, it seems, at least one fin is loosened by the landing. So fiberglass fin joins make sense.
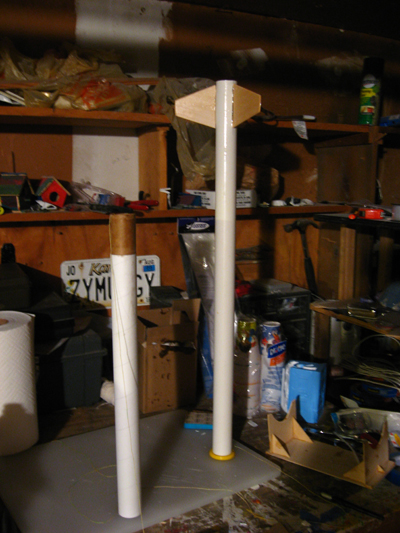
While I was at it, I also epoxied the motor mount, fins and forward shock chord mount into a rocket I haven't yet named. I may glass the fin joins on this one, too, for the practice as much as anything else.
No comments:
Post a Comment